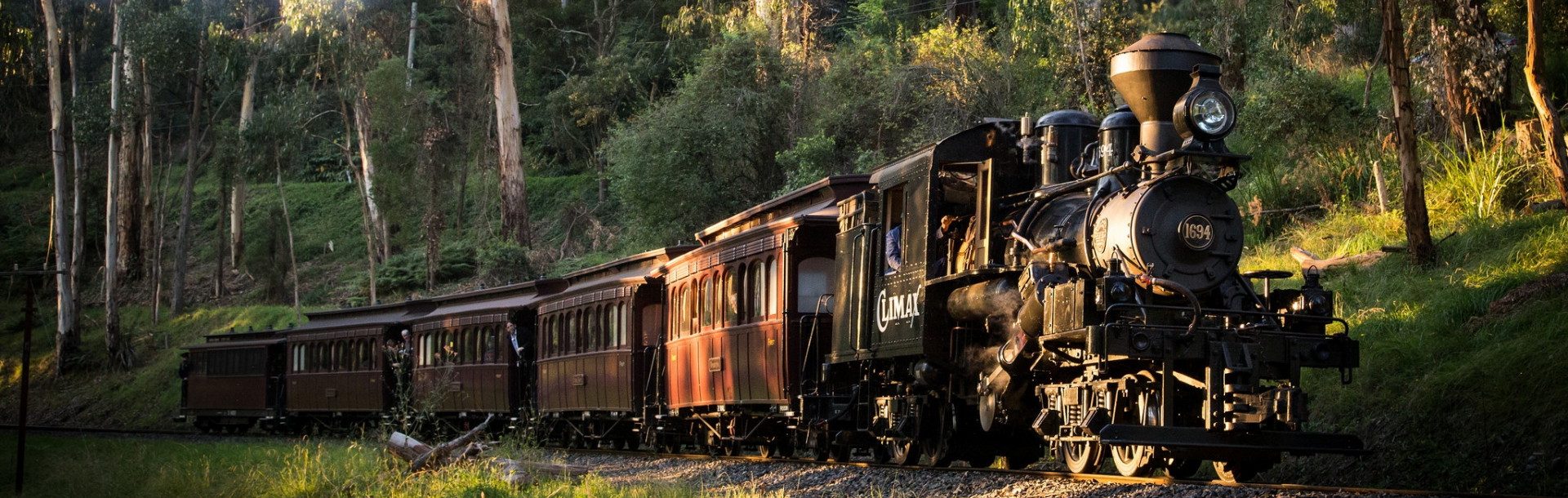
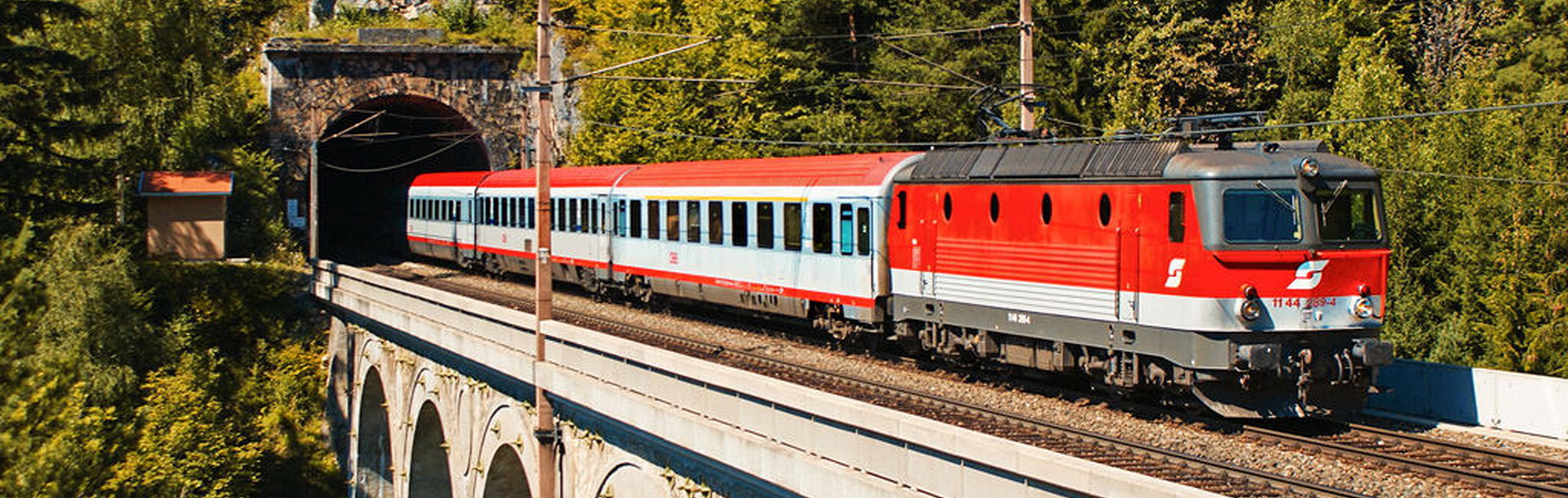
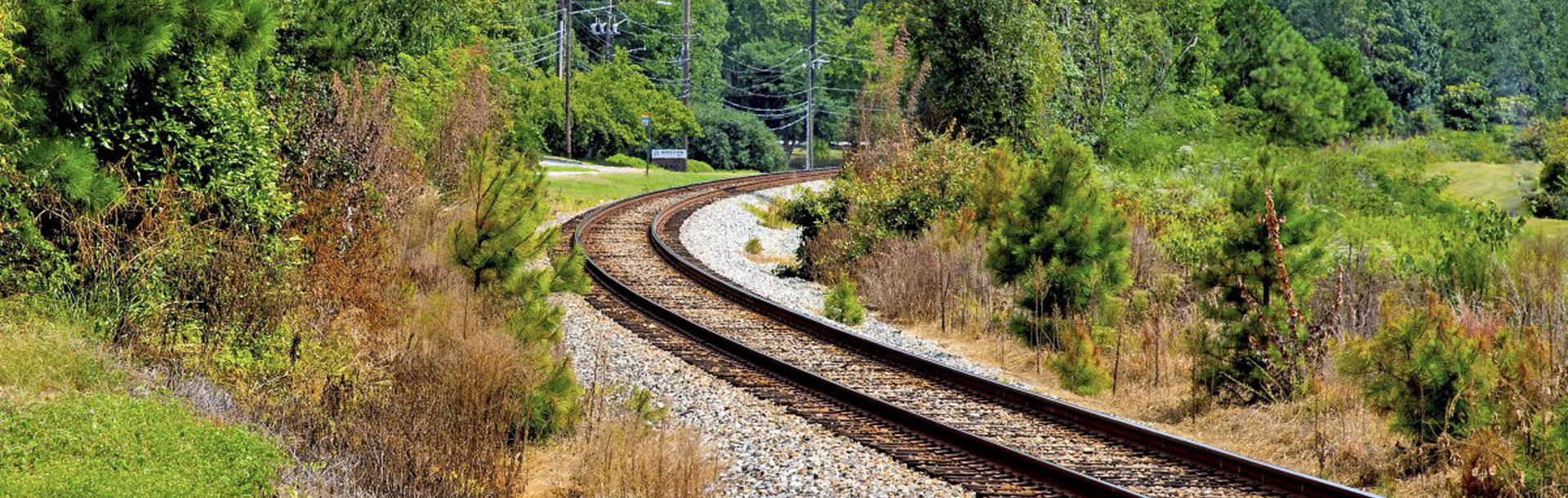
Во многих странах алюминий уже прочно ассоциируется с грузовыми железнодорожными перевозками. Цистерны и танк-контейнеры, вагоны-хопперы – грузовой подвижной состав различного назначения строят из технологичного алюминия и сплавов на его основе. Несколько лет назад к тренду присоединилась и Россия.
Алюминиевая экономика железных дорог
Великая депрессия 1930-х годов и нефтяной кризис начала 1970-х стимулировали внедрение алюминиевых технологий в грузовое вагоностроение, прежде всего в США и Канаде. Так, в 1931 году Aluminium Co. of America выпустила первый в мире полностью алюминиевый грузовой вагон, хоппер для перевозки бокситов, а сегодня порядка 70% грузоперевозок в США осуществляется вагонами из алюминиевых сплавов. Основная причина произошедшего поворота – стремление к максимальной экономической выгоде, приобретающей особое значение в период нестабильности на рынках.
Алюминий на треть легче стали, а по «железнодорожной» шкале у него почти на 20% ниже коэффициент тары (отношение веса тары вагона к его грузоподъемности), в среднем 0,26 против 0,32. При сохранении заданной нагрузки на ось это позволяет перевозить больше грузов тем же количеством вагонов. Выгода тем ощутимее, чем протяженнее маршрут. Неслучайно сегодня в числе лидеров по размерам грузового алюминиевого парка страны-гиганты, включая КНР с ее развитым вагоностроением. «Компактной» Европе приблизиться к этой группе среди прочего мешает ограничение на длину грузовых составов в 700 м против 2000 м, например, в США.
В балансе железнодорожных грузоперевозок учитываются и такие факторы, как скорость состава, потребление энергии и нагрузка на рельсы (от нее зависит соответствующий тариф) при порожнем пробеге. Во всех названных случаях легкость алюминия идет только в «плюс» экономике железнодорожных грузоперевозок
Разнообразие модельного ряда
Номенклатура грузового подвижного состава из алюминия исключительно обширна: универсальные вагоны, полувагоны, зерновозы, хопперы для угля, руды и сыпучих минералов, транспортеры автомобилей, вагоны-цистерны для перевозки концентрированной кислоты. Лидерами на этом направлении являются FreightCar America и китайская корпорация CRRC, крупнейший производитель подвижного состава в мире.
Такое многообразие – следствие многовекторности качеств крылатого металла. Он биологически нейтрален и вместе с тем прочен, устойчив к воздействию агрессивной среды. Одновременно благодаря высокой пластичности из алюминия можно получать листовой прокат, профили, литые детали.
Настоящий прорыв в отрасли обеспечило появление в 1970-х метода экструдирования, подразумевающего продавливание заготовки под высоким давлением для получения профильного изделия. Усовершенствование этой технологии открыло путь к созданию очень габаритных, жестких и вместе с тем легких элементов конструкции, благодаря чему время сборки кузовов сократилось вдвое по сравнению с аналогичными стальными. Одновременно высвободилось большое число занятых на этой операции рабочих, что способствовало удешевлению производства.
Если же требуется скорректировать те или иные свойства алюминия, то здесь на помощь приходят легирующие элементы. Для производства грузовых вагонов сегодня в основном используются сплавы 5ххх (алюминиево-магниевые) и 6ххх (алюминиево-магниево-кремниевые) серии. Первые при умеренной прочности отличаются повышенной коррозионной устойчивостью и великолепно подходят для сварки. Вторые оптимальны для экструдирования. Существенно повысить прочность алюминиевых сплавов позволяет используемый в качестве модификатора скандий.
С точки зрения качества конечного продукта, очень важна и возможность выбора оптимального метода сварки при сборке кузовов из крылатого металла и его производных. Помимо дуговой сварки в защитных газах могут использоваться и такие передовые технологии, как лазерная сварка и сварка трением с перемешиванием. В обоих случаях сокращается число подготовительных операций и обеспечивается высокая скорость соединения элементов конструкции.
Фактор длительного срока службы
В Канаде и США алюминиевые грузовые вагоны не принято окрашивать. Такой способ экономии производственных затрат вполне оправдан. 13-й элемент периодической системы Менделеева обладает эффективным средством самозащиты от коррозии в виде тонкого слоя оксида, образующегося на поверхности металла при контакте с атмосферным кислородом.
Впрочем, ничто не мешает окрашивать алюминиевые элементы вагонов или обрабатывать их ингибиторами ржавчины для еще более эффективной борьбы с коррозией. В любом случае, высокая устойчивость к ней, а также к абразивному износу позволяет до двух раз уменьшить расходы на ремонт и обслуживание алюминиевых грузовых вагонов по сравнению со стальными. При этом у первых гарантированный срок эксплуатации в среднем на 6 лет больше и увеличен сегодня до 4 десятилетий. Но и по достижении максимального срока службы алюминиевые грузовые вагоны сохраняют коммерческую привлекательность: остаточная стоимость составляет до 90% от первоначальной.
Возможности переработки
Алюминий – один из самых экологичных материалов на Земле. На текущий момент около 75% алюминия, произведенного за всю историю металла, продолжает использоваться. Способность к рециклингу позволяет достигать экономии энергии до 95% по сравнению с выплавкой металла из руды. Кроме того, на эту же величину сокращаются и вредные выбросы, что в эпоху ужесточения экологического законодательства сулит ощутимую экономию средств. Металл, отправляемый на переработку может использоваться как в железнодорожной отрасли, так и в строительстве, машиностроении и других сферах промышленности – и это еще одно преимущества алюминия.
Таким образом, более высокая покупная цена грузовых вагонов из алюминиевых сплавов по сравнению со стальными может компенсироваться за счет эксплуатации вагонов на протяжении всего их жизненного цикла, включая затраты на обслуживание, ремонт (алюминиевый грузовой вагон проходит капитальный ремонт максимум один раз) и вторичную переработку.
Развитие в России
В современной истории России первая попытка создать грузовой вагон с алюминиевым кузовом была предпринята в 2010-х. Так, в 2013 году «Промтрактор-Вагон» (ныне – Канашский вагоностроительный завод, входит в концерн «Тракторные завод») выпустил такой хоппер, предназначенный для перевозки зерна и сыпучих грузов. Компоненты для него произвела американская Alcoa: алюминиевые листы, плиты и профили из сплава 1565ч для него были изготовлены в Белой Калитве, стальной крепеж – в США и Великобритании. Однако вагон в серию не пошел.
В 2017 году внедрение алюминия в российском вагоностроении продолжила компания «РМ Рейл», когда сертификацию прошел хоппер-минераловоз модели 19-1244, выполненный из сплава 1565ч. С тех пор были построены 222 вагона этой серии, которые успешно эксплуатирует «Первый промышленный оператор».
Следующий шаг был сделан вагоностроителем в феврале 2022 года, что связано с началом испытаний хоппера модели 19-1299, обладающего по сравнению с предшественником улучшенными техническими характеристиками и потребительскими свойствами. Несмотря на рост полезного объема кузова до 111 куб. метров, массу тары удалось снизить до 21 тонны при одновременном увеличении грузоподъемности до 79 т. Это на 3-8 т больше, чем у стальных аналогов, что дает солидную – до 10% – экономию общей массы на перевозку одной тонны сыпучего груза. Усовершенствована и конструкция вагона. Так, благодаря появлению сплошного загрузочного люка новинка адаптирована ко всем типам погрузочных эстакад.
Кроме того, хопперы модели 19-1299 рассчитаны на более длительный срок эксплуатации. Это результат не только отказа от элементов из черного металла внутри алюминиевого кузова, что исключает его окисление под воздействием агрессивной среды, но и применения нового конструкционного материала: на смену сплаву 1565ч пришел сплав 1581, легированный скандием. Отсюда повышенная на 25% прочность и улучшенная коррозионная устойчивость. Сплав 1581 относится к категории экономнолегированных (добавка скандия измеряется сотыми долями процента), что позволило удержать его стоимость на уровне обычных алюминиево-магниевых сплавов. Также в числе достоинств нового конструкционного материала – способность противостоять охрупчиванию при низких температурах и стойкость к агрессивным средам. Наконец, хорошая свариваемость, в том числе высокопроизводительным методом сварки трением с перемешиванием, делает сплав 1581 еще и очень технологичным.
Опыт применения алюминиевых сплавов в железнодорожном машиностроении обобщен в стандартах:
-
- ГОСТ Р 59598-2021 «Полуфабрикаты для производства элементов кузовов грузового подвижного состава железнодорожного транспорта. Технические условия и сортамент» 1 января 2022 года.
- ГОСТ Р 59849-2021 «Соединения сварные конструкций кузовов железнодорожного подвижного состава из алюминиевых сплавов. Требования к проектированию, изготовлению, ремонту и контролю качества» (вступил в силу 1 апреля 2022 года). Содержащаяся в документах исчерпывающая информация о возможностях крылатого металла позволяет оптимизировать производственный процесс и тем самым снизить затраты изготовителей кузовов вагонов.
Последний упомянутый стандарт достоин отдельного внимания: до его появления требования к методам сварки (сварка трением с перемешиванием), сварным соединениям конструкций кузовов из алюминия для подвижного состава до появления ГОСТ Р 59849-2021 не были собраны в одном документе. Алюминиевая ассоциация, «Арконик СМЗ» и «РУСАЛ» выступили с инициативой разработки документов. Предложение было поддержано Объединением производителей железнодорожной техники (ОПЖТ) и включено в Программу национальной стандартизации в рамках деятельности ТК 045 «Железнодорожный транспорт». Разработчиком выступил ВНИИЖТ.
Данные стандарты позволяют оптимизировать производственный процесс и тем самым снизить затраты изготовителей кузовов вагонов. В результате производители подвижного состава смогут вести работы по увеличению грузоподъемности вагонов и повышению скорости моторвагонного подвижного состава в интересах развития железнодорожного транспорта России.
Источник: Rollingstock
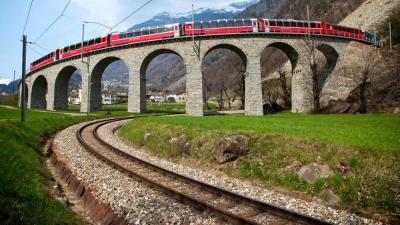
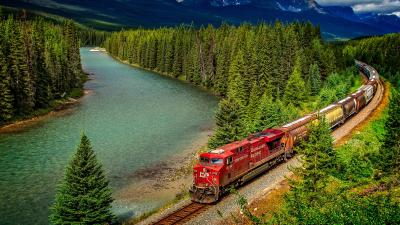
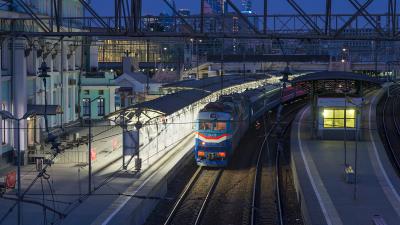